Education
01Pre-Operation Meetings
Before starting operations, the leader explains the operating processes, amount of operation, precaution matters, and any other necessary matters of the day to his/her members. Next, each member carefully listens to the details and starts operating after acknowledging the flow of work and precaution matters on the day. When the member is uncertain, at this time, the members will properly share information with each other. In this way, we build an environment to start the operation in safer conditions.
02KYT (Kiken Yochi Training / Risk Prediction Training) activity (Monthly)
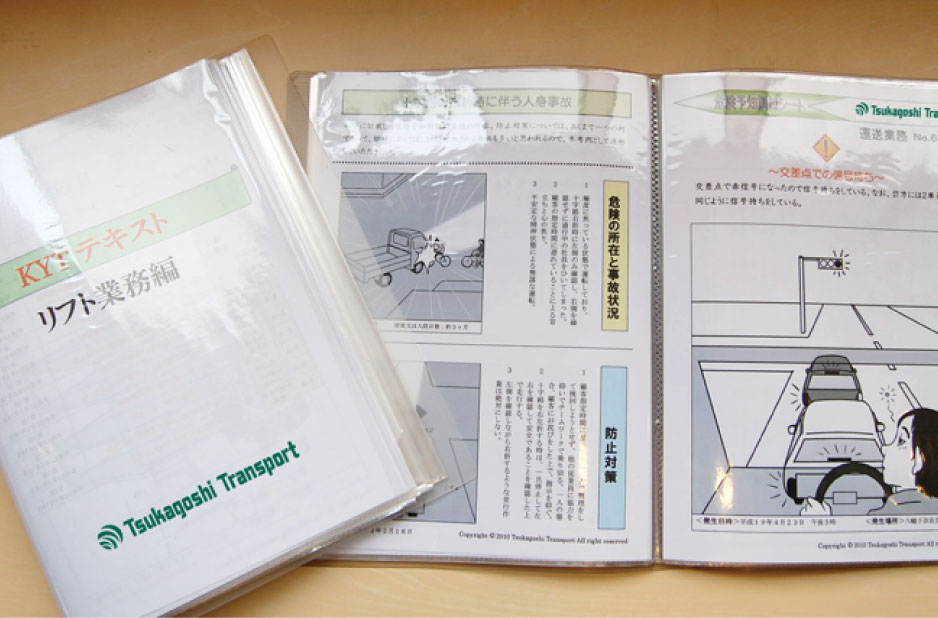
We improve our risk prediction and precaution sense for dangers on a daily basis. We carry on the KYT activity on a monthly basis, which is Risk Prediction Training as training to improve each problem solution ability on site where we operate practically div ided in 4 categories in trucks, forklifts, loading/unloading operations, and office work in small groups of all employees. The skilled supervisors on each operation process make the KYT sheets to test this activity consistent with our practical operations.
03Hiyari Hatto activity (Each time)
"Hiyari Hatto" means almost dangerous, accidental and surprise situations while operating and working. Hiyari means the feeling of cold and fear, and Hatto comes from the sound of surprise or noticing something irregular or dangerous. The most important key point to prevent accidents is that we notice unsafe operations or unsafe workplaces as soon as possible on a daily basis, and we, the entire company, need to solve these problems. So we set up a system to share information with other departments through our Occupational Safety and health Committee, after reporting details of "Hiyari" feeling from the potential dangers or accidents while operating on site to his/her department. Moreover, for transportation, we use drive recorders loaded on trucks and show those recorded "Hiryari" images to our drivers. In this way, our drivers can improve their driving by learning visible education materials with the right side of their brains.
04Training (Each time)
Every February, each Office makes their educational plans for the next fiscal year. In those plans, there are all types of qualifications, or various training such as Truck checking workshops or forklift operation workshops etc. held by external trainers. We focus on improvement of our educational systems on a daily basis. When our Offices request, we plan, establish and carry out this training according to their needs. In this way, we can develop our human resources and can properly respond to rapid and changeable needs from our stakeholders.
05Accident Investigation Meeting (Each time)
We hold accident investigation meetings by replaying actual accident situations to see the actual movement to search for accidental facts. We can establish more efficient countermeasures as a result of this investigation. In addition, all the staff can learn the actual accident situation from simulation experiences from this meeting.
06Study on site (4 times)
We hold study meetings on site for our staff who work in customer services or sales. In these study meetings, we provide 4 step details of "Philosophy", "Manner", "Safety" and "Technology" with a purpose of teaching our company philosophy and practical manners for all our staff.
07Aptitude tests for our drivers (Once a year)
We follow up and acknowledge drivers' health conditions and their changes per year. So we ask our drivers for a general health check-up once a year, as well as a first health check-up for new drivers and an aptitude test for over 65-year-old drivers which is required by law. The test results can make drivers themselves rethink about their features objectively in metacognition ways to drive safely. The test results are also used as educational information sources so that they can educate drivers in necessary ways depending on each drivers' features.
08Competency evaluations
We regularly evaluate our drivers and employees' competency through their qualifications, years of experience, age, aptitude, work experience, and customer evaluation. In this way, we can see their abilities clearly and assign them work based on their competency. Moreover, we use these information sources to make an annual plan for educational training so that we can pull each employee's competency up in stages.